The Advantages of **Infrared Powder Coating Ovens** in the Automotive and Paint Industries
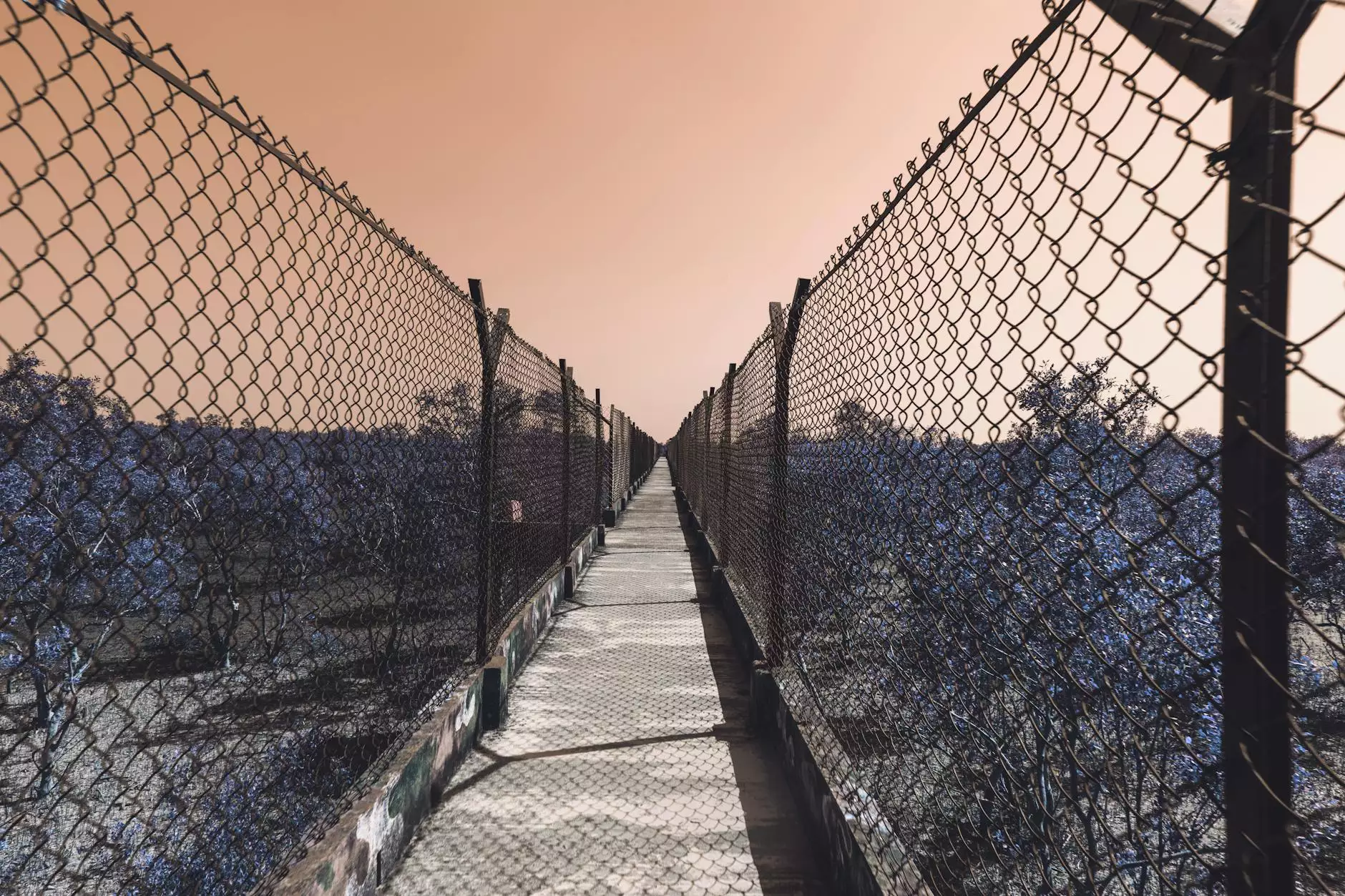
In recent years, the automotive and paint industries have witnessed significant advancements, particularly in coating technologies. One innovation that has garnered attention is the use of infrared powder coating ovens. These specialized ovens are designed to enhance the powder coating process, making it faster, more efficient, and environmentally friendly. In this article, we will delve deeply into the mechanism of infrared powder coating ovens, their benefits, applications, and why they are becoming an indispensable asset in the coating industry.
What is an Infrared Powder Coating Oven?
An infrared powder coating oven is a type of curing oven specifically engineered to utilize infrared radiation for heating, melting, and curing powdered coatings applied to metal substrates. Unlike traditional convection ovens, which rely on hot air, infrared ovens transfer heat directly to the object being coated. This direct heating process results in faster curing times and more even temperature distributions.
How Infrared Powder Coating Ovens Work
The operational mechanism of infrared powder coating ovens involves several critical steps:
- Powder Application: The powder coating is sprayed onto the substrate using an electrostatic gun, which charges the powder particles, ensuring they adhere well to the surface.
- Infrared Radiant Heating: Once coated, the items are placed in the oven. The infrared heaters emit radiant heat that penetrates the powder coating, melting it and preparing it for curing.
- Curing Process: The ideal temperature and time settings must be maintained to allow the powder to fully cure, resulting in a durable and uniform finish.
- Cooling Phase: After curing, the items are cooled down, solidifying the coating and making it resistant to damage.
Benefits of Using Infrared Powder Coating Ovens
The adoption of infrared powder coating ovens presents multiple advantages that can significantly impact operations within the automotive and paint sectors:
1. Enhanced Efficiency
Infrared ovens can drastically reduce curing times. Traditional ovens may take longer due to reliance on hot air circulation. In contrast, the direct heating offered by infrared technology allows for a quicker melting and curing process, thus maximizing throughput and reducing lead times.
2. Energy Savings
By providing targeted heating, infrared powder coating ovens consume less energy compared to conventional ovens. They require less time to reach the desired curing temperature, leading to lower overall energy costs. This aspect is not only economical but also aligns with environmentally sustainable practices.
3. Improved Quality of Finish
The even heat distribution in infrared ovens results in a more consistent and uniform coating. Due to the rapid curing times, the likelihood of defects such as runs, sags, or orange peel finishes is significantly reduced, which is crucial for achieving a high-quality product in the automotive sector.
4. Versatility and Adaptability
Infrared powder coating ovens are versatile and can be adapted for various applications beyond automotive. They can effectively cure different types of powders, including those used in household appliances, furniture, and heavy machinery coatings, making them a valuable asset in diverse industries.
5. Reduced Environmental Impact
Infrared heating systems are more energy-efficient and result in lower emissions compared to traditional ovens. Furthermore, they eliminate the need for harmful solvents that are sometimes used in traditional paint processes, thus contributing to a healthier workplace and environment.
Applications of Infrared Powder Coating Ovens
The versatility of infrared powder coating ovens allows their use across various applications, making them essential in numerous manufacturing processes:
- Automotive Manufacturing: From wheel rims to chassis components, infrared ovens ensure high-quality finishes on numerous automotive parts.
- Furniture and Fixtures: Metal furniture, light fixtures, and accessories benefit from the smooth and durable finish that infrared curing provides.
- Industrial Equipment: Heavy machinery and equipment requiring durable coatings are ideally suited for infrared curing processes.
- Home Appliances: Products such as refrigerators, ovens, and washing machines utilize powder coating for enhanced aesthetics and durability.
Choosing the Right Infrared Powder Coating Oven
Selecting the appropriate infrared powder coating oven for your specific needs is pivotal to ensuring optimal performance. Consider the following factors:
- Size and Capacity: Assess the size of the items you need to coat and choose an oven that can accommodate them efficiently.
- Temperature Range: Ensure the oven can achieve and maintain the necessary temperature range required for the specific powder coatings you intend to use.
- Heating Technology: Evaluate the type of infrared heaters (e.g., shortwave, mediumwave) used in the oven for versatility and performance.
- Energy Efficiency: Opt for models designed to optimize energy use while maintaining performance standards.
- Manufacturer Reputation: Research the credibility and track record of manufacturers, like those featured on autocoatindia.com, to ensure reliable equipment.
Conclusion
In conclusion, the integration of infrared powder coating ovens within the automotive and paint industries not only improves operational efficiencies but also elevates the quality of the final products. With their energy-saving capabilities, reduced curing times, and versatility, they offer manufacturers a competitive edge in today’s fast-paced market. As companies strive for excellence and sustainability, investing in infrared technology is proving to be a strategic move for the future.
For more information about the wealth of options available in infrared powder coating ovens and to explore how they can enhance your operations, visit Autocoat India today!