Unlocking Potential: The Importance of Die Casting Molds in Metal Fabrication
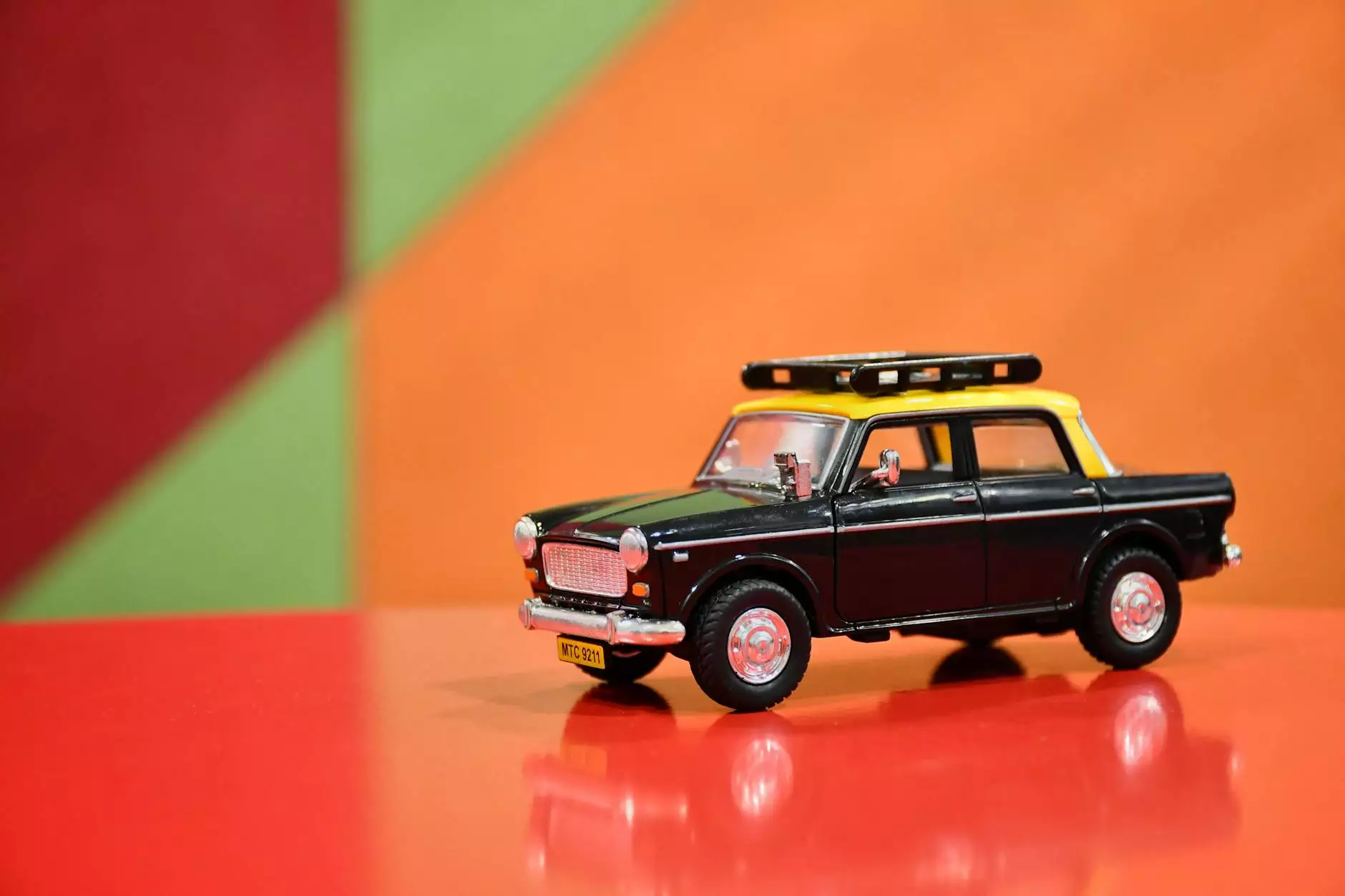
Die casting molds are an essential component in the metal fabrication industry, enabling businesses to produce high-quality metal parts with incredible efficiency and precision. For metal fabricators, understanding the ins and outs of die casting molds can greatly enhance their manufacturing processes and product offerings. This article will delve into the intricacies of die casting molds, highlighting their types, benefits, applications, and how to choose the perfect mold for your needs.
What is Die Casting?
Die casting is a manufacturing process that involves forcing molten metal into a mold to create intricate shapes and components. It is widely used in various industries, including automotive, aerospace, consumer goods, and electronics. The key to successful die casting lies in the design and fabrication of the die casting mold.
Types of Die Casting Molds
Die casting molds can be classified into various types depending on their construction and the methods used. Here are the primary types:
1. Single Cavity Molds
Single cavity molds are designed to produce one part at a time. They offer simplicity and are ideal for low-volume production runs, making them a great choice for prototypes and small batch manufacturing.
2. Multi-Cavity Molds
Unlike single cavity molds, multi-cavity molds can produce multiple identical parts in a single cycle. This design increases efficiency and is more cost-effective for larger production volumes.
3. Family Molds
Family molds are designed to produce different parts simultaneously, often featuring varying shapes and sizes. They are ideal for manufacturers looking to optimize their production processes by creating multiple components in one shot.
4. Permanent Mold Casting
In permanent mold casting, reusable molds are made from materials like steel or iron. This method allows for higher-quality finished products due to the molds' heat retention properties, which results in better cooling rates and enhanced material integrity.
Benefits of Using Die Casting Molds
Investing in high-quality die casting molds offers numerous advantages for metal fabricators:
1. High Precision and Accuracy
Die casting molds provide exceptional dimensional stability, allowing for the production of intricate and precise metal components. This level of accuracy is crucial in industries where tight tolerances are required.
2. Enhanced Surface Finish
Parts produced using die casting methods typically exhibit a smooth finish, reducing or even eliminating the need for extensive post-processing. This enhances the aesthetic appeal and functional benefits of the final product.
3. Cost Efficiency
Although the initial investment in die casting molds can be significant, they yield cost savings over time due to reduced material waste and high production rates. The efficiency of the process results in lower labor costs and shorter lead times.
4. Versatility
Die casting molds can accommodate various metals, including aluminum, zinc, and magnesium. This versatility allows manufacturers to choose the best material for their specific application, enhancing the performance and durability of the final product.
Applications of Die Casting Molds
The applications of die casting molds are vast and varied, highlighting their importance in multiple sectors:
1. Automotive Industry
In the automotive sector, die casting molds are used to produce components such as engine blocks, transmission cases, and wheels. The lightweight and strong parts manufactured through this process contribute significantly to vehicle performance and efficiency.
2. Aerospace Components
The aerospace industry relies on die casting molds to create intricate parts that must meet strict regulatory standards. Components manufactured through die casting often feature complex geometries and exceptional strength-to-weight ratios, necessary for flight operations.
3. Electronics
Electronics manufacturers utilize die casting molds to produce housings, heat sinks, and other components. The high precision and clean finishes achieved through die casting are essential for the functionality and aesthetics of electronic devices.
4. Consumer Goods
From kitchen utensils to bicycle parts, die casting molds play a pivotal role in creating durable and aesthetically pleasing consumer products. The ability to produce high volumes of identical parts efficiently makes it a favored choice among manufacturers in this sector.
Choosing the Right Die Casting Mold
Selecting the appropriate die casting mold is crucial for achieving optimal results. Here are several factors to consider:
1. Design Complexity
The complexity of the part design will influence the type of mold required. Intricate designs may necessitate advanced multi-cavity or family molds to ensure efficient production.
2. Production Volume
High production volumes typically benefit from multi-cavity molds to maximize output. Conversely, low-volume production may only require single cavity molds to minimize initial costs.
3. Material Selection
Understanding the material properties and specifications is vital when choosing a mold. Different metals require different mold designs and materials, so consider the specific requirements of your application.
4. Budget Considerations
While quality is paramount, it is essential to balance between mold quality and budget constraints. Investing in high-quality molds can yield long-term savings due to reduced maintenance and higher production efficiencies.
Conclusion
In conclusion, die casting molds play a vital role in the metal fabrication industry, offering precision, efficiency, and cost-effectiveness. By understanding the various types of molds available and their specific applications, businesses can make informed decisions that enhance their manufacturing processes. At deepmould.net, we specialize in providing top-notch die casting molds tailored to fit a variety of needs, ensuring exceptional quality and customer satisfaction. As the demand for superior metal casting increases, investing in reliable die casting molds is a step towards securing your business's success in a highly competitive market.