Understanding Machining Lathe Parts Factories
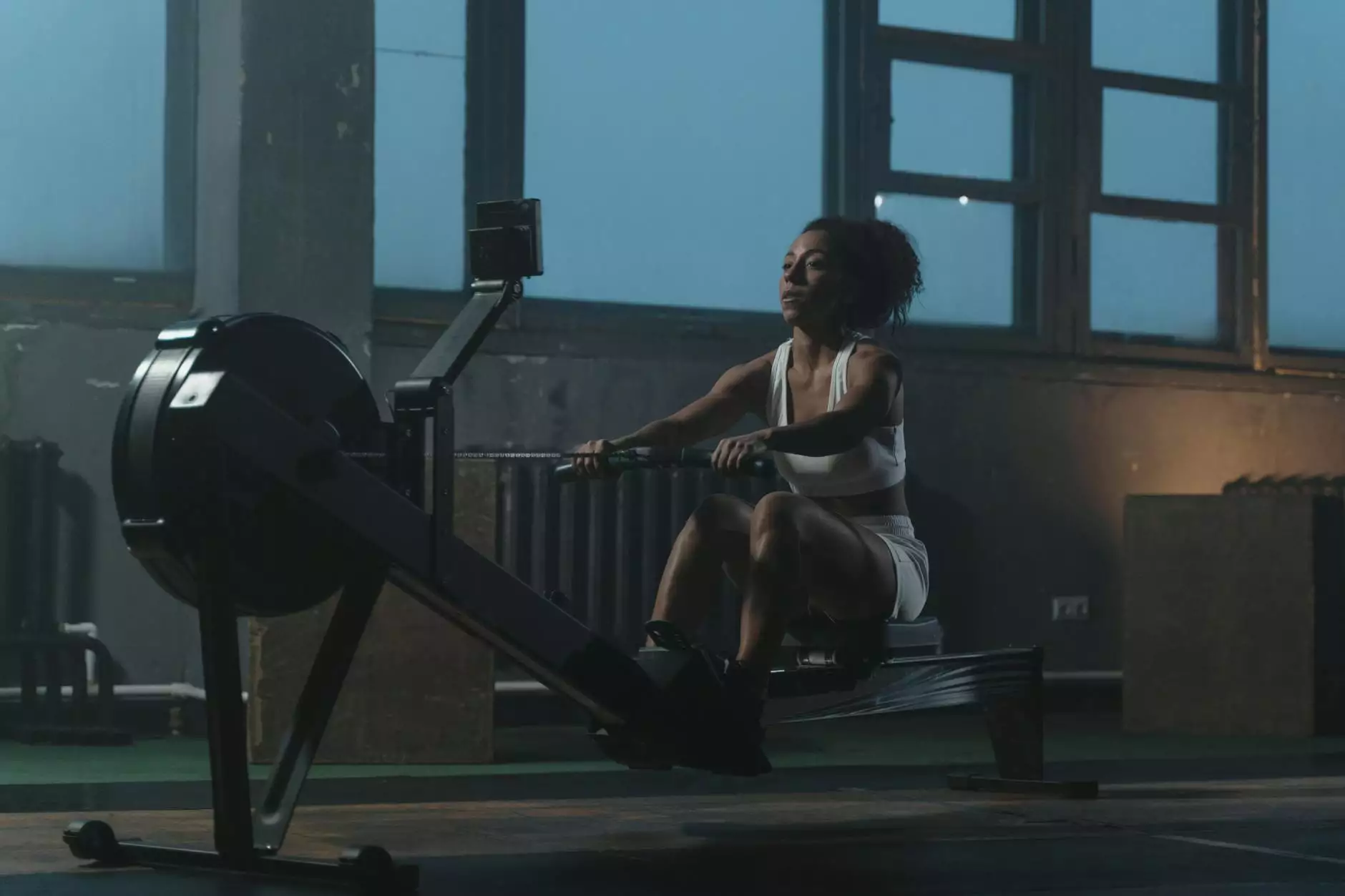
In today's fast-paced industrial landscape, machining lathe parts factories play an essential role in the manufacturing sector. These factories are pivotal in producing precision-engineered components that are crucial for various industries, including automotive, aerospace, and machinery manufacturing. This article delves deep into the world of machining lathe parts, highlighting their significance, the processes involved, and the future trends that are shaping this dynamic field.
The Role of Machining Lathe Parts in Various Industries
The production of lathe parts is fundamental to numerous sectors. Here are some ways in which these components are utilized:
- Automotive Industry: Machining lathe parts are used to manufacture engine components, transmission parts, and more.
- Aerospace Industry: Precision machined parts are critical for aircraft engines, landing gear, and other vital systems.
- Machinery Manufacturing: Components like gears and shafts produced through lathe machining are vital for various machinery operations.
- Electronics: Specialized lathe parts are used in creating casings and internal components for electronic devices.
What Are Machining Lathe Parts?
At its core, lathe machining involves the rotation of a workpiece against a tool, allowing for the precise shaping of metal parts. There are several types of lathe parts produced, each with unique functions:
- Shafts: These are cylindrical components that transfer power or motion.
- Spindles: A critical component in machines, spindles hold rotating tools.
- Housings: These parts enclose and protect other components, often found in machinery and electronics.
- Flanges: Used to connect two parts together, flanges are essential in piping and mounting applications.
The Manufacturing Process in Machining Lathe Parts Factories
The manufacturing process in machining lathe parts factories typically involves several stages to ensure precision and quality. Here is an overview of the process:
1. Material Selection
The first step is selecting the appropriate material, which can range from steel to aluminum, depending on the desired properties of the final product.
2. Machining Setup
After selecting the material, it is set up on the lathe machine. This involves securing the workpiece and calibrating the machine.
3. Turning Process
The lathe machine begins the turning process, where it rotates the workpiece while cutting tools shape it to meet specifications.
4. Finishing Operations
After turning, finishing operations such as sanding, polishing, or additional machining are performed to achieve the final dimensions and surface finish required.
5. Quality Control
Rigorous quality control checks are essential to ensure that each manufactured part meets industry standards and specifications. This often involves precision measuring tools and techniques.
Advantages of Machining Lathe Parts Factories
The advantages of utilizing tooling and manufacturing processes in machining lathe parts factories are manifold:
- Precision: Lathe machining allows for high precision and accuracy in manufacturing parts.
- Customization: Factories can create bespoke components tailored to specific needs.
- Efficiency: Automated lathe processes enhance production speed and reduce labor costs.
- Versatility: Lathes can work with a variety of materials, making them suitable for different applications.
Challenges Faced by Machining Lathe Parts Factories
Despite the advantages, machining lathe parts factories face several challenges:
1. Skilled Labor Shortage
There is a growing demand for skilled machinists, which can present challenges in maintaining high-quality production.
2. Technological Advancements
Staying up-to-date with the latest technology in machining can be both an opportunity and a challenge, requiring investment in new machines and training.
3. Environmental Regulations
Factories must comply with strict environmental regulations, leading to increased operational costs.
Future Trends in Machining Lathe Parts Manufacturing
As industry demands evolve, so too do the methods and technologies used in machining lathe parts factories. Some emerging trends include:
1. Automation and Robotics
The integration of robotics in machining processes is revolutionizing the industry, providing improved efficiency and precision.
2. Advanced Materials
Developing new materials that can withstand higher stress and wear opens avenues for enhancing product quality.
3. 3D Printing Integration
The fusion of traditional machining with additive manufacturing (3D printing) allows for complex designs that were previously difficult to achieve.
Conclusion: Embracing the Future of Machining Lathe Parts Factories
In conclusion, machining lathe parts factories are integral to the modern manufacturing ecosystem. Their ability to produce high-precision components is vital across a multitude of industries. As technology advances and new materials are developed, these factories are poised for growth, adapting to meet the demands of a rapidly changing industrial landscape. Investing in modern technology, skilled labor, and sustainable practices will be the key to thriving in this competitive field. The future looks bright for machining lathe parts, and businesses that recognize their importance will likely see substantial success.