Understanding the Centrifugal Pump Graph: Key Insights for Optimal Performance
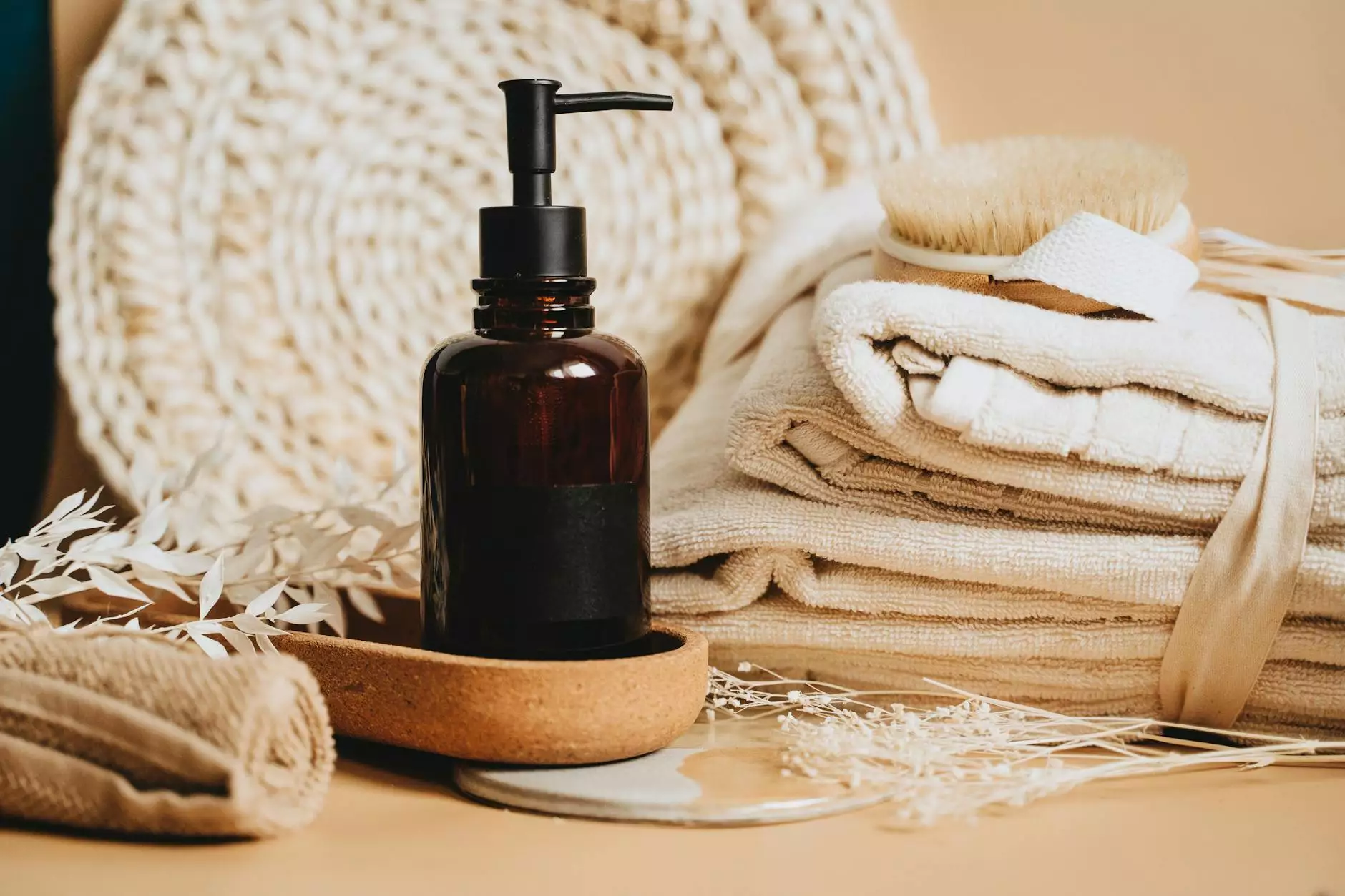
The Significance of Centrifugal Pumps in Modern Industry
The centrifugal pump is one of the most essential components across various sectors, including auto repair, farm equipment repair, and structural engineering. These pumps play a crucial role in transferring fluids, particularly in processes requiring high efficiency and reliable service.
Whether it’s moving water for agricultural irrigation, circulating coolant in automotive repairs, or ensuring structural integrity through fluid management, the centrifugal pump is indispensable. Understanding its operation and efficiency is vital for professionals in these domains.
How Does a Centrifugal Pump Work?
Centrifugal pumps operate on a simple yet effective principle: they convert rotational energy into hydrodynamic energy. The core components of a centrifugal pump include the impeller, volute, and bearing system:
- Impeller: The rotating component that imparts velocity to the fluid.
- Volute: The casing that converts the velocity energy of the fluid into pressure.
- Bearing System: Ensures smooth operation and minimizes wear and tear.
When the impeller rotates, it generates a centrifugal force that pushes the fluid outward. This action results in a decrease in pressure at the suction side, which draws more fluid into the pump. The continuous motion creates a steady flow of fluid, making centrifugal pumps highly effective for various applications.
The Importance of the Centrifugal Pump Graph
A centrifugal pump graph is essential for visualizing the performance characteristics of a pump. By analyzing this graph, engineers and technicians can assess how a pump behaves under different conditions. Key elements often included in these graphs are:
- Flow Rate: The volume of fluid the pump can move, typically measured in GPM (gallons per minute) or LPM (liters per minute).
- Head: The height to which the pump can raise the fluid, usually represented in feet or meters.
- Efficiency Curve: Shows the efficiency of the pump at different flow rates.
- NPSH Required: Represents the pressure required at the suction side to avoid cavitation.
Interpreting the Centrifugal Pump Graph
Understanding the centrifugal pump graph involves analyzing these performance metrics to ensure that the pump operates within the desired parameters. Here’s how to interpret the key components:
1. Flow Rate vs. Head
The relationship between flow rate and head is crucial for determining a pump's performance range. As flow rate increases, head generally decreases. This is important for selecting the right pump for a specific application; an optimal operating point should be identified where the pump works most efficiently.
2. Efficiency Curve
This curve indicates how effectively the pump converts input power into hydraulic energy. Higher efficiency means lower operational costs. It's vital to choose a pump that operates near its best efficiency point (BEP) for maximum performance.
3. NPSH Required vs. Available
Understanding Net Positive Suction Head (NPSH) is critical to avoid cavitation, which can damage the pump. The graph must be analyzed to ensure the NPSH available exceeds the NPSH required throughout the pump's operating range.
Applications of Centrifugal Pumps
Centrifugal pumps find diverse applications across several industries, including:
- Auto Repair: Used in cooling systems for vehicles, ensuring efficient circulation of coolant.
- Agriculture: Essential for irrigation systems to deliver water from various sources.
- Construction: Used in dewatering applications, fluid transport during construction activities.
Factors Influencing Pump Performance
The performance of a centrifugal pump can vary based on numerous factors including:
- Fluid Properties: Density, viscosity, and temperature can significantly influence pump performance.
- Impeller Design: The design and size of the impeller affect fluid velocity and pump capacity.
- System Layout: The configuration of pipes and fittings can create additional friction and resistance affecting the overall efficiency.
Maintaining Optimal Pump Performance
To ensure that centrifugal pumps operate at peak efficiency, regular maintenance and monitoring are crucial. Here are some practices to maintain optimal performance:
- Regular Inspections: Conduct periodic checks to identify potential issues such as leaks, noise, or vibration.
- Check Alignment: Ensure that the pump and motor shafts are properly aligned to prevent unnecessary wear.
- Monitor Vibration: Use vibration analysis to identify misalignments or imbalances.
- Lubrication: Maintain proper lubrication of bearings and other moving parts to prevent failure.
Choosing the Right Centrifugal Pump
Selecting the appropriate centrifugal pump for a specific application involves several considerations:
- Determine Fluid Characteristics: Understand the properties of the fluid being pumped to choose compatible materials.
- Calculate Required Flow Rate: Estimate the desired flow based on system requirements.
- Evaluate Head Requirements: Assess the total dynamic head needed, factoring in vertical lift and friction loss.
- Consider Environmental Factors: Ensure the pump can operate efficiently within the environmental conditions of its application.
Conclusion
The centrifugal pump graph is a powerful tool in understanding and optimizing pump performance across various industries. From auto repair to agricultural applications, having a firm grasp of how to read and analyze these graphs can lead to better decision-making and enhanced operational efficiency. Regular maintenance, correct sizing, and awareness of fluid dynamics can ensure that your centrifugal pumps run smoothly and effectively, contributing to the overall success of your projects.
In summary, as industries continue to evolve, the role of centrifugal pumps will only become more significant. Understanding their mechanics, performance curves, and operational requirements may just be the key to ensuring sustainability and efficiency in your business.