The Importance of Air Pressure Units in Business and Engineering
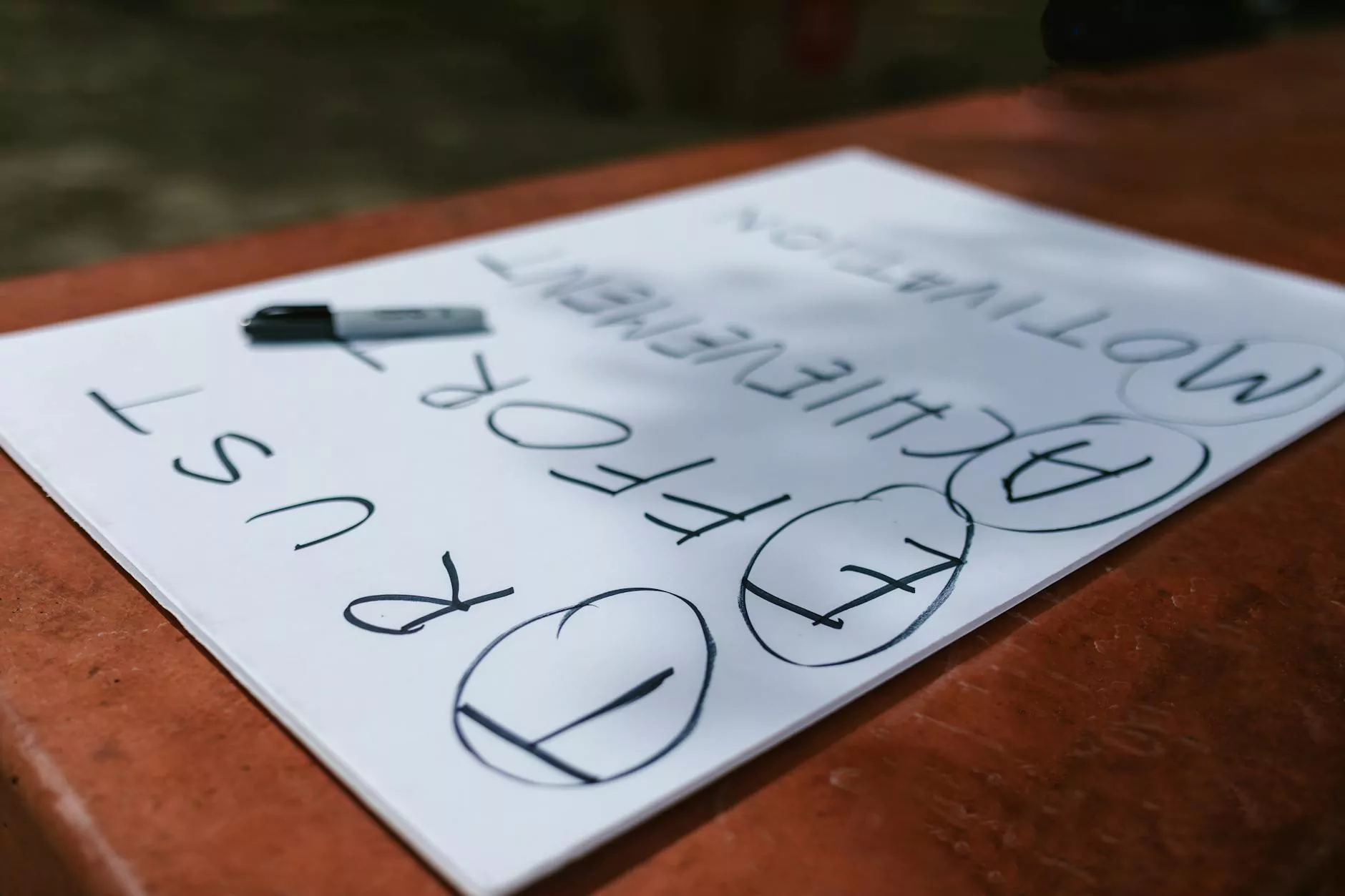
In today’s modern landscape, understanding the mechanics of various systems is essential for businesses in sectors such as auto repair, farm equipment repair, and structural engineering. One critical aspect that spans across these fields is the concept of air pressure units. This article will explore the significance of air pressure units, their applications, and their impact on the efficiency and efficacy of operations within these industries.
Understanding Air Pressure Units
Air pressure units are measures of the pressure exerted by air, which is vital for numerous applications across various industries. Common units of air pressure include:
- Pascals (Pa)
- Bar
- Atmospheres (atm)
- Millimeters of Mercury (mmHg)
- Pounds per Square Inch (psi)
Each of these units plays a significant role in understanding and measuring the pressure needed for equipment and processes to function correctly. The choice of unit often depends on the industry standard and the specific application involved.
The Role of Air Pressure Units in Auto Repair
In the auto repair sector, air pressure units are crucial for several reasons:
1. Tire Pressure Monitoring
Maintaining proper tire pressure is vital for safety and fuel efficiency. Mechanics utilize psi to measure tire pressure accurately. A tire that is under or over-inflated can lead to:
- Poor handling and braking performance
- Increased tire wear
- Decreased fuel economy
Using an air pressure gauge, technicians ensure tires are inflated to the manufacturer-recommended specifications, enhancing safety and efficiency.
2. Air Conditioning Systems
The functionality of automotive air conditioning systems heavily relies on proper air pressure levels. Mechanics measure bar or psi to diagnose system efficiency. Regular maintenance checks for refrigerant levels can prevent breakdowns and enhance the comfort of the vehicle's occupants.
3. Brake Systems
Modern vehicles employ pneumatic brake systems that depend on air pressure to function effectively. Constant monitoring and adjustment of pascals is necessary to ensure a safe and responsive braking system. A decrease in air pressure in brake systems can lead to catastrophic failures, making proper measurement crucial.
Air Pressure Units in Farm Equipment Repair
The agricultural sector is another domain where air pressure units prove invaluable:
1. Pneumatic Equipment
A significant amount of farm equipment operates using pneumatic systems, such as seeders, harvesters, and sprayers. Here, air pressure units help determine the operational effectiveness of these machines. For example, psi measurements are used to control the pressure levels in pneumatic tools, ensuring optimal performance and longevity.
2. Irrigation Systems
In irrigation, maintaining the correct air pressure is essential for the efficient delivery of water. Many systems rely on pressurized air to distribute liquids effectively. By using atmospheres as a unit of measure, farmers can determine the optimal pressure settings to maximize irrigation efficiency, preventing wastage and ensuring crop health.
3. Safety and Precision
Handling heavy machinery requires utmost safety, which can be greatly influenced by air pressure units. Properly calibrated pressure systems prevent equipment failure and accidents, which is why farmers need to monitor these parameters regularly.
Significance of Air Pressure Units in Structural Engineering
In structural engineering, understanding air pressure units can be critical during the design and construction phases:
1. Wind Load Calculation
One of the key aspects of structural engineering is assessing wind loads on buildings and structures. Engineers employ pascals to calculate how much pressure wind exerts on various surfaces. This information is crucial for designing safe and compliant structures that can withstand environmental forces.
2. HVAC Systems
Heating, ventilation, and air conditioning (HVAC) systems play a vital role in the comfort and efficiency of buildings. Understanding the air pressure dynamics within these systems using pascals and bar measurements allows engineers to design systems that optimize airflow and energy consumption.
3. Quality Assurance and Testing
Pneumatic pressures often affect how construction materials react under various conditions. Before any construction, tests must be performed to ensure materials can withstand certain pressures, allowing engineers to determine the appropriate air pressure units during testing processes.
The Interconnection of Air Pressure Units Across Industries
The understanding of air pressure is not only limited to individual industries but also crosses boundaries, impacting multiple fields. As we’ve seen, the accurate measuring and applying of air pressure units can significantly enhance performance, safety, and effectiveness across various applications.
Best Practices for Using Air Pressure Units
In order to effectively utilize air pressure units, businesses can adopt the following best practices:
- Regular Calibration: Instruments used to measure air pressure need to be calibrated regularly to ensure accuracy.
- Training and Awareness: Employees must be trained to understand the significance of various air pressure measurements tailored to their specific area.
- Safety Procedures: Adhering to safety standards when working with pneumatic systems is crucial for preventing on-site accidents.
Conclusion
The concept of air pressure units is deeply embedded in the functions of various sectors, notably in auto repair, farm equipment repair, and structural engineering. The influence of proper air pressure measurement and management cannot be overstated. As businesses continue to innovate and enhance operational efficiencies, the understanding and application of air pressure units will remain a pivotal part of keeping industries safe, effective, and competitive.