Understanding Dip Molding Materials in Electronics and Medical Supplies
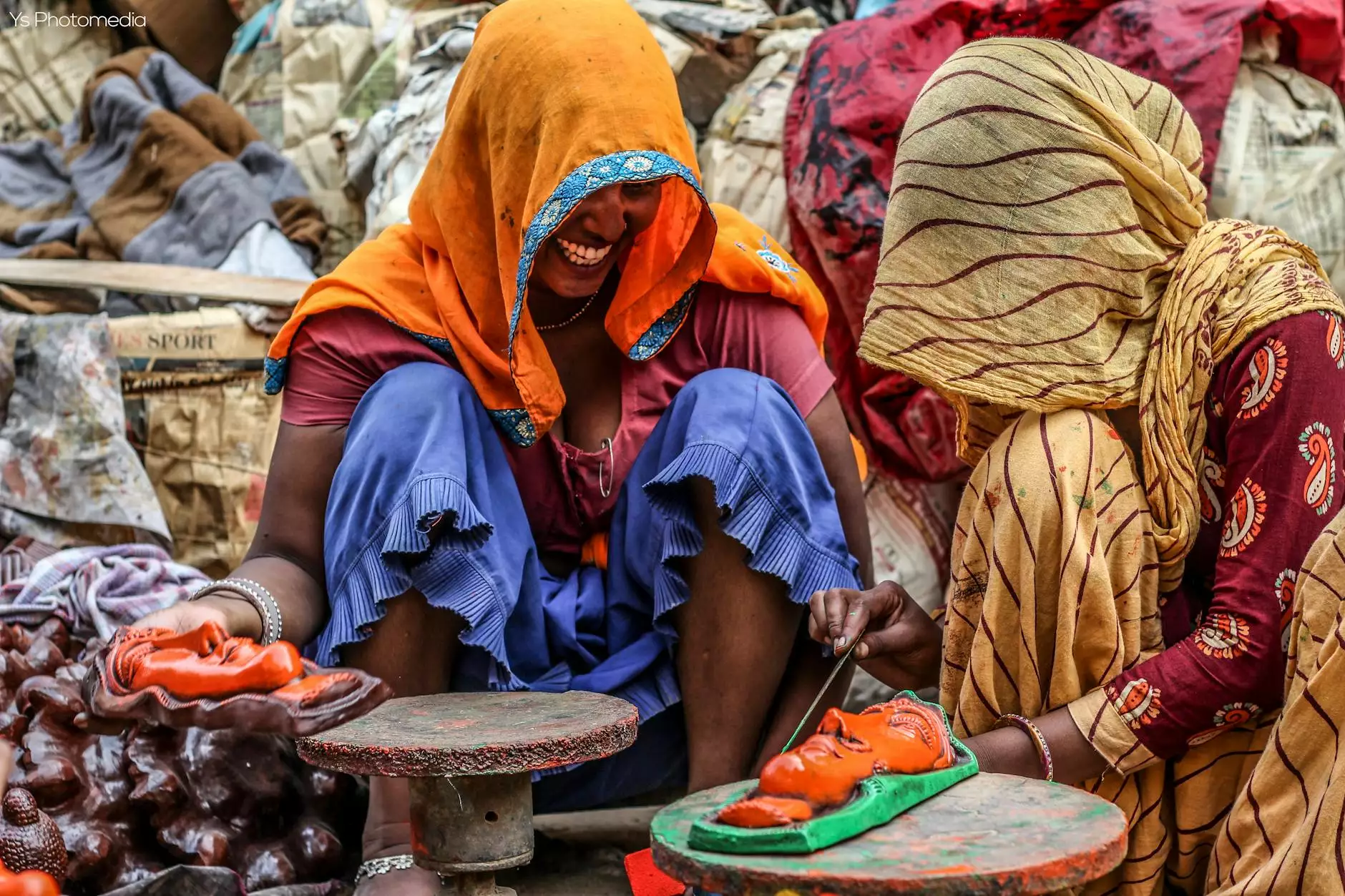
Dip molding, a highly versatile manufacturing process, has garnered significant attention across various industries, especially in electronics and medical supplies. In this article, we will delve deep into the world of dip molding materials, exploring their properties, applications, advantages, and their pivotal role in these sectors.
What is Dip Molding?
Dip molding is a simple yet effective manufacturing technique that involves immersing a mold into a liquid material, typically a polymer. After immersion, the mold is withdrawn, allowing the liquid to coat the mold’s surface. As the polymer cures, it forms a solid layer, producing a molded part.
The Process of Dip Molding
The dip molding process can be broken down into several key steps:
- Preparation of the Mold: The mold may be made from various materials and needs to be cleaned and prepared to ensure proper adhesion of the dip molding material.
- Dipping: The mold is submerged in the heated liquid polymer, allowing for an even coating.
- Cooling: After removal from the bath, the mold is cooled to allow the material to solidify.
- Demolding: Once cured, the molded part is extracted from the mold.
The Varieties of Dip Molding Materials
Understanding the different types of dip molding materials is crucial for selecting the right product for your specific application. Below are some of the commonly used materials:
- PVC (Polyvinyl Chloride): Known for its flexibility and durability, PVC is one of the most popular materials used in dip molding. It is resistant to environmental factors and ideal for various applications.
- Rubber: Often used when a textured finish is required, dip molded rubber provides excellent grip and is commonly applied in medical devices.
- Polyurethane: This material is known for its high tear strength and abrasion resistance, making it suitable for demanding applications.
- Silicone: With its high-temperature resistance and biocompatibility, silicone is widely used in medical applications.
- Latex: Latex materials are utilized for creating soft and flexible parts, particularly in the medical and consumer markets.
Applications of Dip Molding in Electronics
In the electronics sector, dip molding materials play a vital role in protecting and insulating electrical components:
1. Wire Coating
Dip molding is extensively used to coat wires, creating a protective layer that insulates electrical connections and prevents damage from moisture and dust.
2. Switches and Connectors
The durability of dip molded coatings makes them ideal for switches and connectors, where protection from environmental factors is crucial.
3. Custom Electronic Components
Due to the versatility of dip molding, manufacturers can create custom electronic components tailored to specific requirements, enhancing the efficiency and performance of devices.
Applications of Dip Molding in Medical Supplies
The medical industry benefits immensely from dip molding processes, with applications that require precision and safety:
1. Medical Device Coatings
Dip molding provides a smooth finish on medical devices, ensuring they are free from defects and ready for safe use in clinical settings.
2. Grip Handles
Medical tools often require comfortable grips, which can be achieved through dip molding, offering a soft-touch surface that enhances usability.
3. Custom Molds for Specific Instruments
For many medical instruments, custom molds produced through dip molding can optimize functionality and provide the necessary performance characteristics.
Benefits of Using Dip Molding Materials
The advantages of employing dip molding materials in manufacturing are numerous:
- Cost-Effectiveness: Dip molding is generally less expensive than alternative manufacturing techniques, making it an economical choice for mass production.
- Versatility: With a variety of materials and colors available, dip molding can produce high-quality parts for assorted applications across industries.
- Customization: Manufacturers can easily customize the thickness, texture, and properties of the molded materials to suit specific needs.
- Environmental Resistance: Many dip molding materials are resistant to chemicals, moisture, and UV exposure, enhancing the longevity of the products.
- Simplicity of Process: The dip molding process is relatively straightforward, allowing for robust production lines and reduced lead times.
Quality Considerations in Dip Molding
While dip molding offers many advantages, ensuring quality throughout the process is critical:
1. Material Selection
Choosing the right dip molding materials is essential. Factors such as chemical compatibility, flexibility, and hardness must be assessed based on the application.
2. Mold Design
The design of the mold significantly influences the final product. Proper design can facilitate consistent thickness and quality across all molded parts.
3. Process Parameters
Control over temperature, immersion time, and cooling duration is crucial. Variations in these parameters can lead to inconsistencies in the final products.
Innovative Uses of Dip Molding Materials
1. Consumer Products
The consumer goods industry is increasingly utilizing dip molding for products such as tool handles, kitchen utensils, and sports equipment.
2. Automotive Components
Dip molding materials are also making waves in the automotive sector, providing protective coatings for electrical connections and enhancing user comfort in various controls.
3. Aerospace Applications
In aerospace, dip molded parts are employed where lightweight, durable, and resistant materials are essential.
The Future of Dip Molding Materials
As technology continues to evolve, so too will the applications for dip molding materials. Innovations in material science may lead to:
- Biodegradable Materials: In response to environmental concerns, the development of biodegradable dip molding materials may emerge.
- Smart Materials: Integration of technology into dip molded products could lead to smart devices that respond to environmental conditions.
- Advanced Customization: Enhanced manufacturing technologies may allow for even greater customization options.
Conclusion
In summary, dip molding materials are essential to the electronics and medical supplies sectors, offering remarkable versatility and benefits. From protecting electronic components to creating safe, user-friendly medical devices, dip molding plays a crucial role in modern manufacturing. As the future unfolds, the possibilities for innovation in this area remain vast, promising exciting developments for industries that rely on high-quality materials and manufacturing processes.
Nolato.com stands at the forefront of this industry, providing expertly made dip molded products tailored to meet the needs of various applications. By leveraging the advantages of dip molding, manufacturers can ensure they are equipped with high-quality materials that enhance performance and durability.